Bothar's cutting head innovation
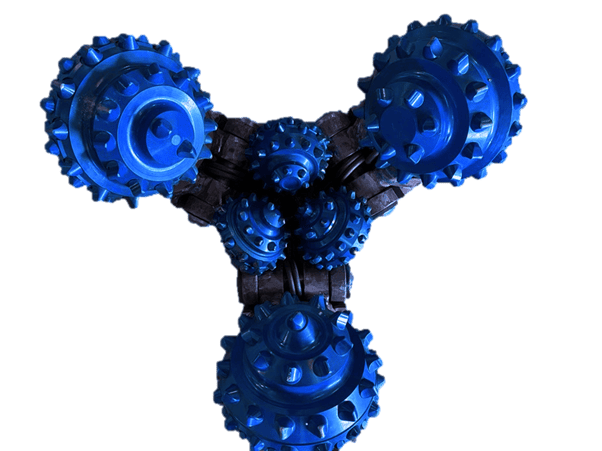
Method: Bothar Built
In house designed and fabricated: Unique retractable bi-directional cutting head
Location: Wakerley, QLD, Australia
OVERVIEW
The trenchless industry in Australia continues to grow and the need to provide customised solutions becomes vital for a leading subsurface contractor.
Recognising the need for advanced solutions to meet the growing demands of modern infrastructure projects, Bothar Boring has led the way in the innovation department with its vast fleet of in-house designed and fabricated ‘Bothar Built’ equipment.
Now, the company is breaking new ground with its latest specialist-built cutting head.
Bothar has an exceptional team of industry leading experts and equipment manufacturing specialists that turn ideas and concepts into cutting-edge solutions to overcome limitations of conventional methods.
In recent times, Bothar has experienced an increase in requests for installations where there is an inability to provide a retrieval shaft.
Bothar refers to this practice as ‘blind boring’ and it had been an obstacle on the company’s radar for some time.
When the company was approached for advice on providing a suitable method to install 19 x 102m canopy tubes under a live railway without the ability to use a retrieval shaft, the team was confident they could deliver.
There are limited trenchless methods which could deliver accuracy over such lengths.
As such, Bothar embarked on a mission to develop an innovative solution to directly install the required 500mm steel case, in rock up to 60Mpa without an exit shaft, with pinpoint accuracy, while ensuring the ground was always supported.
The result was a custom designed specialised bi-directional retractable cutting head which hadn’t been utilised on this size of installation.
Using Bothar’s in-house design and fabrication facilities, the cutting head was designed, built, and tested within a matter of weeks.
The experimental cutting head was deployed to site and proved to be extremely effective.
The tight program constraints meant that Bothar had to install two canopy tubes at a time, adding additional complexity to the delivery.
Bothar successfully completed the canopy tube installation and was able to accelerate the pace of the project with its bespoke cutting head.
The unique cutting head consists of three 13 ¾-inch and three 9-inch tri-cone type TCI cutters on a 50mm backing plate with water portability and outer cutters spring loaded on a 40mm greaseable solid bar hinge.
A laser guided vacuum system was used to achieve tight design tolerances at significant lengths.
The modified head was developed to ensure the tunnel is always supported by the installation of steel casing in the unlikely but possible case of ground movement.
The cutting head has since been used successfully on several projects in adverse, mixed ground conditions up to 200Mpa.
Furthermore, tackling other obstacles such as ‘blind boring’ into service manholes is now no problem with the use of this cutting head, changing the landscape of underground construction.
Bothar’s ability to utilise its vast trenchless experience to innovate such a design is backed by its inhouse workshop facility.
This gives Bothar Boring an additional advantage in the ever-evolving trenchless arena for future works.